Management system
In 2022, the Company updated its key strategic objectives in health and safety for 2023–2025. Efforts in this area are primarily focussed on achieving an industry average injury rate and zero‑rate fatalities.
Heads of production sites are personally responsible for the life and health of each of their subordinates. Injury and industrial safety metrics weigh between 10% and 35% in their individual KPIs. Failure to prevent a fatality blocks performance bonuses. In addition, team KPIs for all employees include injury rate and FIFRFatal Injury Frequency Rate, the number of fatalities per million hours worked. reduction by 20% or more, with 10%—25% weighting.
The Audit Committee at the Board of Directors deals with industrial safety matters. The Committee reviews management reports on industrial safety performance every quarter, hears reports on causes of accidents, measures taken to prevent similar accidents in the future, and disciplinary actions taken against the employees at fault.
The Company’s Health, Safety, and Environment Committee, led by the Senior Vice President – Operational Director, is focussed on improving performance and accountability in health and safety. The Committee meets quarterly at various production sites of the Group.
Certifications and audits
In 2023, Nornickel’s health and safety management system updated its certificate of conformity through a successful audit.
Bureau Veritas Certification, the certification body, described the Company’s OHS management system as mature and well‑established and found that the corporate systems of Nornickel’s audited companies met the relevant requirements of the standard. The Company’s strengths cited by the auditor include the ongoing safety culture development project; use of IT solutions and risk‑based approach tools; contractor management; and focus on continuous improvement of the health and safety management system.
As at the end of 2023, 49%By average headcount. of Group companies maintained health and safety certification ISO 45001
A total of 53 audits involving the Group’s production site heads and their deputies took place in 2023. The audits included a comprehensive inspection of safe practices as well as equipment condition, maintenance, and operation.
Work‑related injuries
In 2023, the Company continued implementing its Building Risk‑Based Thinking Skills project aimed at revising the health and safety incident reporting process to improve transparency and quality of incident classification. These efforts resulted in faster response times and unlocked more opportunities for further analysis of workplace incidents. Root cause investigation and identification were also overhauled, which contributed to more effective incident prevention in the future.
In 2023, the Company’s lost time injury frequency rate (LTIFR) slightly rose from 0.58 to 0.65 but remains below the industry average. Nornickel continued to improve mine safety by deploying its Anti-collision proprietary solution and enhancing its machinery and personnel tracking systems.
Tragically, five fatal accidents were recorded at the Company in 2023. All accidents were thoroughly investigated, with the resulting reports submitted to the Board of Directors and action plans developed to eliminate their root causes. The Company continues to improve the quality of its incident investigations while also reinventing its occupational safety communications with employees. The Group sees fatality‑free operations as its strategic priority.
Following the investigations of structure collapse incidents in the Kola and Norilsk Divisions, the Company has structured a procedure for performing maintenance and repair of ore conveyors subject to the results of sensor‑based non‑destructive testing, set up a technical council to assess the quality of repair, and decided to replace wooden roofing of vertical mine workings with concrete roofing.
To prevent collision of employees with self‑propelled diesel equipment, the Company fits its mining machinery with the Anti‑collision system that stops the vehicle if a pedestrian is detected in a hazardous area. Nornickel also installs walkways, traffic lights, and spherical mirrors. Common requirements have been developed for vehicle and pedestrian traffic plans in underground workings, and safety zones set up for remote control load‑haul dumper (LHD) operators.
Following the investigation into a self‑propelled drilling rig fall from height, Nornickel has developed a standard fence for vertical mine workings with change in elevation; visualised hazardous areas; provided operators of underground machinery with up‑to‑date traffic plans; and piloted underground navigation solutions.
Contractor safety
Contractors’ work‑related injuries
The Company’s procedural documents on industrial safety – regulations, policies, corporate standards, Golden Rules of Safety – also apply to our contractors.
In 2022, Nornickel reviewed the general terms and conditions related to occupational health in its contracts with contractors to emphasise the achievement of zero fatalities and zero breaches of industrial safety rules.
All tasks performed by contractors in highly hazardous conditions are carried out in line with corporate standards. Work permits must contain safety requirements to be met when organising and performing work. The Company checks compliance with these requirements during each shift. Prior to the commencement of any work, contractor employees are required to receive induction and targeted briefings on occupational health, including safety measures.
At its sites, Nornickel holds regular joint inspections for compliance with safety requirements and H&S committee meetings involving contractor representatives. In the event that contractors fail to comply with safety requirements, they are fined.
Safety culture
The Company continuously improves its H&S system elements. These changes cover all production units of the Company – from mining ore to making metals.
To keep employees well‑informed about safety measures, the Company regularly develops and updates its guides, videos, presentations, and other visuals highlighting the most important guidance to protect life and health in various situations or when performing certain types of work.
A culture of safety begins with mindful behaviour and leadership demonstrated by each employee. Nornickel continues to run the Developing Risk‑Based Thinking project across all of its mines while also growing its train‑the‑trainer programme. Since 2023, 20 Group enterprises run an initiative that encourages employees to take ownership of workplace safety. This initiative has served as a basis for a bonus programme that encourages employees to adopt safer ways of working and offers additional rewards for showing initiative and taking responsibility. Bonuses are also awarded to employees who complete training in safe working practices offered by internal coaches and later successfully identify new risks and suggest mitigants. The bonus size depends on the extent of employee’s involvement in risk mitigation and is between RUB 5 thousand and RUB 10 thousand. Once these bonuses were introduced, most identified risks were eliminated as employees adopted a more responsible and mindful approach to health and safety requirements, thereby improving the overall manufacturing culture and employee engagement. In 2023, 449 employees earned bonuses to a total of RUB 3.5 million for identifying workplace risks.
The Company has in place a formal procedure for refusing a task if exposed to a risk. Such refusal does not entail any sanctions against the employee. Complaints or suggestions can be anonymously submitted by each employee via the Corporate Trust Line speak‑up programme. On top of this, employees can ask questions and get feedback from managers of different levels at working meetings, huddles, etc.
Emergency preparedness
In line with Russian laws, Nornickel’s facilities remain prepared at all times for any emergencies, including emergency containment and response. This is vital, as the Company operates more than 300 hazardous production facilities that rely on hazardous substances for their operational processes.
Emergency preparedness system
- Every enterprise has in place on‑site emergency response plans
- Contracts with professional emergency rescue services and organisations are maintained across the Company’s footprint
- Auxiliary mine rescue teams are set up and take regular training in near‑real‑world settings
- Our employees take emergency response training, with drills conducted on a regular basis
- Provisions are made for emergency response at hazardous production facilities
- Emergency surveillance, warning, communication, and response support systems operate across facilities
Monitoring of violations
Nornickel has developed and operates a multi‑tiered H&S monitoring system, with ad hoc, targeted, and comprehensive H&S inspections.
In 2022, the incident reporting procedure was changed to accelerate responses, and the incident classification system was improved to enhance further analysis. The investigation and root cause identification process was significantly transformed to prevent future incidents.
In addition, the Company conducts regular behavioural safety audits. The prevention and control team has identified and disciplined close to 8 thousand non‑compliant employees, including by partially or completely stripping them of their bonuses.
Employee training
The Company is committed to ensuring its people have all the necessary knowledge, skills, and competencies to perform their duties in a safe and responsible manner.
Training starts right after a new employee is hired, with a health and safety induction and subsequent on‑the‑job briefings. Briefings are then repeated regularly in accordance with the existing corporate programmes. All Group employees also regularly take online industrial safety trainings followed by tests. There are also interactive training courses for employees in main occupations. In 2023, over 57 thousand Group employees were covered by these trainings and briefings.
A project to establish a train‑the‑trainer programme for safety culture moved into an active phase during the year. In 2023, a total of 3,111 Dynamic Risk Assessment trainings were held involving about 45 thousand employees as well as 1,151 Behavioural Safety Audit trainings involving over 13 thousand employees.
Prevention of occupational diseases
To minimise the risk of occupational diseases, Nornickel operates the Sulphur Project aimed at reducing sulphur dioxide emissions, takes effective healthcare measures considering both workplace and personal risk factors, and encourages healthy lifestyle.
Regular health monitoring of employees is key to preventing occupational diseases. Employees undergo mandatory pre‑employment, regular, and ad‑hoc medical examinations at the Company’s expense during their employment at the Company. Production enterprises have dedicated medical aid posts to perform pre‑shift health checks and provide medical assistance on request.
The Company protects employees from negative workplace factors by providing collective and personal protective equipment while also offering more effective work and rest schedules and better workplace amenities. All employees have a mandatory meal break during their shifts.
Special examinations at occupational pathology centres are provided to employees exposed to hazardous substances. Employees working in contaminated conditions are provided with free‑of‑charge wash‑off and decontaminating agents. Employees exposed to hazardous or highly hazardous conditions are provided with free preventive nutrition, milk, or equivalent food products.
Corporate healthcare
The Company is focussed on the availability of medical care for its employees and their families. To provide them with quality and timely healthcare services both at medical centres and enterprises, the Company set up Nornickel Corporate Health Centre.
Nornickel’s first corporate medical centre opened in Norilsk in 2021 to service patients under the voluntary health insurance (VHI) programme. Today, it provides 249 types of medical services across 13 primary care specialties. The average appointment wait time ranges from seven days to one month, which confirms the high local demand for quality medical care.
In 2023, the Company continued to roll out its healthcare network to the production sites in the Norilsk Industrial District and on the Kola Peninsula. Shop‑level healthcare departments were set up to prevent diseases and provide quality medical care to employees directly on‑site.
An MRI department was commissioned at the Kolsky Health and Spa Centre in Monchegorsk, which provides 86 types of medical services across five specialties. In Dudinka, the Dudinka Medical Centre was opened. It currently offers 174 types of medical services across nine specialties, with a therapist, physical therapist, massage nurse, and nursing staff available on a permanent basis. Specialist doctors come to the centre weekly from central outpatient facilities.
Since 2021, 30 medical facilities have been put into operation, with a total of more than 2.2 million medical examinations and over 34 thousand procedures delivered. At the moment, medical centres in the Talnakhsky and Kayerkansky Districts of Norilsk and in Monchegorsk are being prepared for launch.
The Company also rolled out its Digital Healthcare programme to deploy innovative IT solutions in medical technology. The programme was introduced at Zapolyarye Health Resort in 2021 and in Norilsk in 2022. A mobile app was developed and launched, enabling employees to access their medical records, make an appointment with a doctor, and get all the information they need about the clinics’ services. Nornickel continues to digitise key medical documents and set up self‑diagnostic systems and a disease risk assessment system.
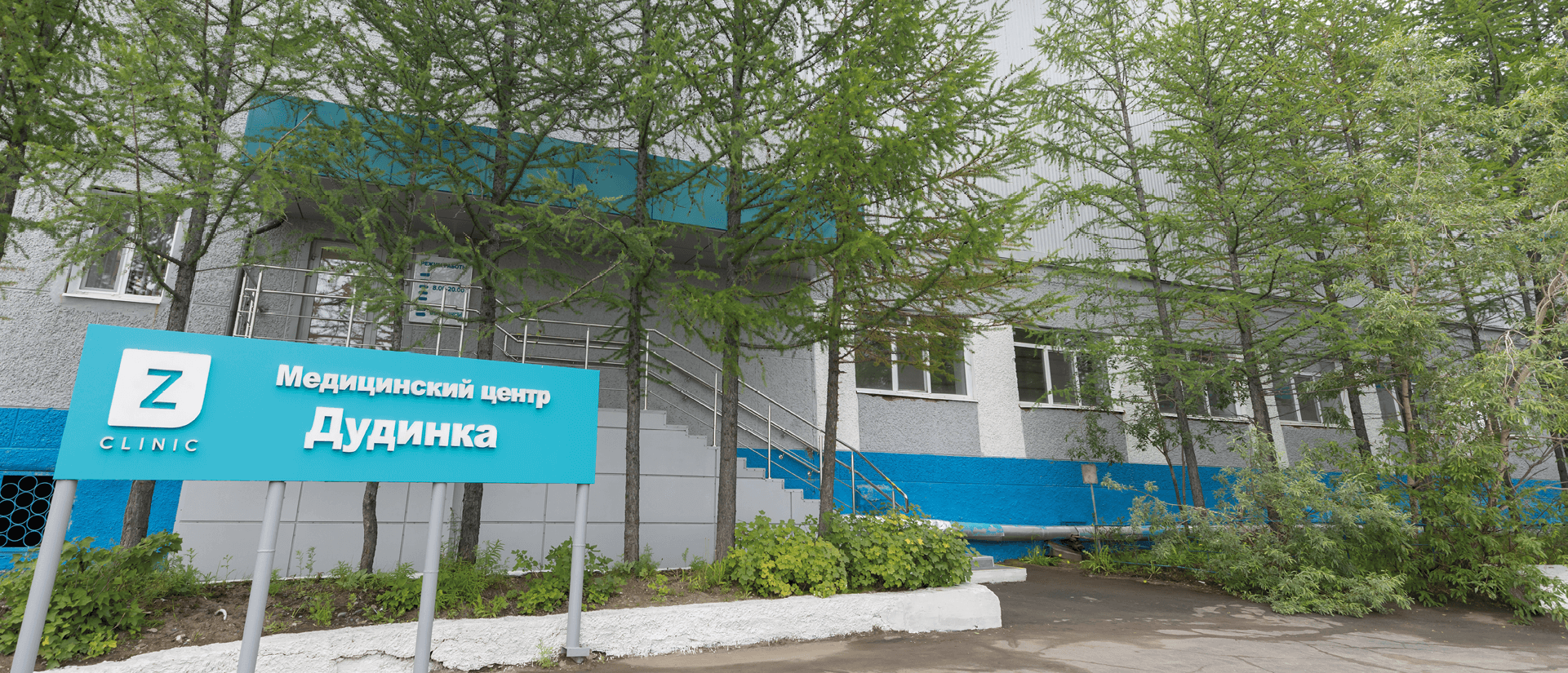