Contribution to the UN SDGs
Nornickel relies on innovative solutions such as artificial intelligence (AI) and machine learning (ML) at all stages of its production process, from exploration to smelting, to streamline processes and make its operations safer for people and the environment.
The Company’s goal is not only about research, development, and deployment of promising technologies but also about building the Company’s own R&D capabilities, shaping internal policies, and fostering a culture of high‑tech developments.
Gipronickel Institute, which makes part of the Group and is one of Russia’s largest research and design centres for mining, concentration, and metallurgy, is Nornickel’s core R&D platform.
In 2023, its continuous converting technology was patented in South Africa, and Roast–Leach–Electrowin technology in Kazakhstan and China.
Industrial safety technology
Video analytics
To maintain a safety culture at its operations, Nornickel is actively adopting solutions that use AI‑enabled video analytics. The Company operates a proprietary solution to monitor the use of personal protective equipment (PPE) by operational staff.
The AI‑enabled solution continuously monitors workwear usage on the shop floor, including safety helmets with chin straps buckled up, safety goggles, and other protective equipment. Specialists are also training the system to monitor and record the use of a safety harness when working at height. If an employee violates the rules for using personal protective equipment, the system will generate a violation card and send it to the line manager, who will review each case and make a decision. The card is then submitted to a coordinator from the Occupational Health and Safety Department for final review. Once the decision is approved, the department head conducts a behavioural safety audit of the employee.
New safety incident detection models were also added (detecting unauthorised access to hazardous areas, detecting open fire, etc.) in 2022, and the solution was integrated with personnel tracking and face recognition modules. During the same year, the Norilsk Division launched pilot tests of a video analytics system at its industrial facilities. In 2023, Nornickel launched a PPE enforcement system at Bystrinsky GOK.
Emergency monitoring
A prototype of a system to monitor the areas under gantry cranes was successfully launched in 2023. The system projects a laser beam to illuminate a hazard warning zone under the crane so as to increase operational safety and monitor the presence of people around load handling areas. The Company is planning to further roll out the system to 15 cranes in Trans‑Baikal Division.
Environmental protection technologies
Reduction in emissions
In 2023, Nornickel and subsidiary IT company Norsoft launched a joint project to develop an automated emissions accounting system enabled by digital process twins. The project has been included into the list of approved projects for substituting Russian alternatives for foreign software and into the development roadmap for the New Industrial Software high‑tech area. On top of this, the project is on the priority list and is expected to bring significant environmental benefits.
In 2023, an initiative to improve the environmental conditions and reduce air pollutant emissions was launched as part of the Sulphur Project at Nadezhda Metallurgical Plant. The project provides for sulphur dioxide recovery into sulphuric acid to be then neutralised with limestone into gypsum cake, which will be stored in a gypsum storage facility.
The Company continues its research into producing artificial anhydrite from gypsum to be used in solidifying backfill mixtures in mines. The solution will eliminate the continuous expansion of the gypsum storage facility and phase out the production of natural anhydrite.
The Company is considering the launch of a WGCPWGCP – wet gas cleaning plant. Retrofit project to boost the performance of the wet gas cleaning plant’s pulp filtration section at Copper Plant. Currently, Vanyukov furnace off‑gases undergo consecutive wet cleaning from dust and then are cooled, while pulp is filtered, with the cake returned to the melting stage.
Tech‑enabled construction
Construction management platform
Nornickel is testing a digital platform that provides a common data environment for specific construction projects based on updatable digital models of buildings and structures. Norilsk renovation projects have been selected for piloting the platform.
Although construction is not the Company’s core business, its investment programme includes the construction of industrial facilities, homes, and social infrastructure. Digital technologies enable monitoring of funds allocated for these initiatives, accelerating data exchange between contributors, and identify design errors and deviations from design.
Laser scanning‑based analytics
This is one of the most promising technologies for digital control over construction and installation. Ground‑based LiDAR scanning is used at each construction stage to automatically detect deviations between the construction project and its initial 3D model.
The solution is used in the Norilsk renovation programme as well as at mining facilities of the Polar Division.
Technology in operations
Geological data analysis
The Company is working on creating a single digital platform that will support end‑to‑end automation of core business processes at mining enterprises: exploration, drilling, sampling, mining, rock bolting, etc. Such a platform will ensure that high‑quality reliable process data are accessible at all levels of the Company’s management, and accordingly, enable faster and better management decision making.
The project’s IT product was presented at the 19th Mining Forum and the 2023 MINEX Russia forum, winning a finalist diploma in the MineDigital category.
PGM production technologies
The Company has developed a technology to recover precious metals from converter matte sent to the Harjavalta nickel refinery. The crushed converter matte is replaced with a non‑magnetic fraction from the first milling stage to reduce the amount of WIP PGMs by 1.8 tonnes.
Nornickel has also designed solutions to produce refined platinum, palladium, gold, and silver. The Kola Division is planning to pilot a precious metals refining technology section, which will enable the Company to build in‑house capabilities in this area and update core process parameters and parameters of product and semi‑product quality using actual concentrates with a view to launch in‑house refining projects at later stages. The technologies provide for annual processing of 36 tonnes of concentrate and production of at least 3 tonnes of platinum and at least 12 tonnes of palladium powder.
Palladium Centre
To date, the Centre’s portfolio comprises more than 20 new palladium products offered through projects at various development stages:
Hydrogen power. A range of Nornickel products under development is meant to support hydrogen energy, where palladium can be used at every step of the production chain: hydrogen extraction from water, production from gas, transportation, and directly in fuel cells. The Company has obtained catalyst samples for electrolysers with 30% of iridium substituted by palladium, which offer a threefold increase in activity compared to existing commercial alternatives. Another innovation was synthesised catalyst samples for fuel cells with 25% of platinum substituted by palladium, which offer over double the activity of existing commercial alternatives (the plan is to substitute up to 80%). Catalyst samples are currently being tested by respected foreign partners, after which they will be sent to end consumers.
New chemistry. The Company is working on a range of products for new chemistry technologies, such as catalysts for glycolic acid synthesis for cosmetology, FDCA for biodegradable packaging, and elements for water disinfection. The samples are expected to move to customer testing in 2024.
Solar power. Research in this area is focused on developing a prototype of a new thin‑film solar cell using palladium chalcogenide, which will improve efficiency and reduce cost compared to existing silicon‑, tellurium‑, or copper‑based cells.
The Company also joined efforts with research institutes for fundamental research to unlock the potential of palladium in longer‑term applications, such as superconductors, supercapacitors, microelectronics and spintronics devices, battery technology, and medical devices.
Nornickel is actively building a partner network of experts and customers, conducting R&D jointly with institutes and laboratories in Russia and beyond, and engaging closely with potential customers in the Asian market to accelerate the commercialisation of new products.
More than 100 new palladium‑containing materials are planned to be developed in the next 5 to 10 years. The Company estimates that new uses for palladium will add at least 40 tonnes of demand for the metal by 2030.
Production management optimisation
As part of diagnosing the current production flow and building a project portfolio, the Company has decided to stabilise the parameters of the initial melting charge. To this end, Nornickel has developed digital assistants which make recommendations on the process flow.
In 2023, the Company launched a project for streamlining the management of concentrate charge blending at the concentrate dewatering and storing shop (CDSS) and the flash smelting furnace (FSF). This will optimise the pyrometallurgical process through stabilising the nickel sulphide concentrate charge while reducing the standard deviation of the total amount of non‑ferrous metals in the FSF’s matte from target levels.
The effectiveness of this approach has been confirmed by pilot tests completed so far. The Company is planning to include expectations of improved process parameters into the efficiency improvement programme. The technical effect of these transformations will be tracked during the first half of 2024, and then the solutions will be put into commercial operation with support from contractors.
Machinery video monitoring
In 2023, the Company developed a software suite to monitor the operation of mining machinery, including autonomous haul trucks, load‑haul‑dumpers, mine cars, tipping devices, and self‑propelled drilling rigs. The suite accurately tracks machinery movements and load through video images and offers video tagging functionality to speed up the acquisition of data sets and leverage the expertise of mine experts to improve accuracy. At the time of writing this Report, the suite was in the testing stage. Four prototypes have already been developed, slated for testing in the Norilsk Division’s mines in 2024.
Ore Flow project
The Ore Flow project enabled by computer vision and launched in the Kola Division unlocks new opportunities for better management of underground rail transport and ore logistics. The system detects underload or ore buildup, analyses fractions and ore water content. Ore quality can be assessed using infrared light, enabling video analysis even in dust conditions. The system also locates individual pieces of machinery in a mine by monitoring loading and unloading locations and transport routes.
All detection models built for the system make part of an integrated solution and were being piloted at the Severny Mine at the time of writing this Report. The system is planned to be further rolled out to other mines of the Norilsk Division.
Improving drilling quality
In 2023, the Company, continued the automation of drilling preparations through a solution based on visual navigation and digital beacons. At the first stage, the application displays tips for the operator by projecting a laser beam, ensuring better drilling and reducing drilling problems. Going forward, we are planning to develop an in‑house solution, which could be automated and rolled out across our entire fleet of self‑propelled drilling rigs regardless of their manufacturer.
The system’s tests confirmed that machinery tracking is highly accurate. Equipment scale models were later built, a self‑propelled drilling rig was inspected to connect the equipment for correct operation, and terms of reference were prepared to develop a software and hardware suite prototype.
The development of the prototype and two equipment sets is expected to be completed before April 2024, with pilot tests slated for April–May. The decision on commercial operation will be taken based on the performance during the test period.
Modelling underground blasting
In 2023, the Company launched a project to model underground drilling, aimed at reducing the share of rock dilution with waste rock and concrete during drilling and cleaning as well as cutting drilling and blasting costs.
Computer modelling, with rock parameters factored in, enables highly accurate predictions of blasting outcomes while optimising target drilling and blasting patterns. At the time of writing this Report, the Company selected the optimal software solution, assessed the technical and economic benefits from its adoption, and collected data for modelling and conducting full‑scale pilot tests, slated for the first half of 2024.
The Company plans to validate that the model’s performance meets the technical and economic targets and roll it out across all mines of the Polar Division before the end of the year.
Modelling open‑pit blasting
In 2022, the Company launched a project that models rock displacement during open‑pit blasting. This solution will enable more accurate ore displacement predictions while reducing metal losses when recovering the rock.
Currently, the model enables ore displacement predictions using both actual data on drilled wells and explosives used, as well as target values, to select the optimal design of the block to be blasted. Six blasts were carried out based on model data in 2023, and the technical impact was verified.
The Company has already launched the process of procuring software for a full‑scale rollout of the solution at Bystrinsky GOK. During 2024, Nornickel is planning to train staff on the new functionality.
Concentration optimisation
Research was conducted and preparations are underway for deploying wet magnetic separation for enhanced recovery of magnetic pyrrhotite from tailings of the Company’s concentrators. At the time of writing this Report, the initiative’s economic feasibility was confirmed, with the expected impacts of an increase in nickel output by 1.5 kt and PGMs by 602 kg over three years.
Norilsk Concentrator piloted a flotation plant to further deploy ejector flotation machines and boost throughput roughly by 100–150 ktpa of ore.
Research was conducted on ionometric mapping and optimisation of pulp ionic content during flotation of copper‑nickel ores at the Company’s concentrators. It was established that reagent consumption can be effectively regulated by using ion‑selective electrodes. Tests will be continued to validate the result on winter pulps; in case of success, the Company expects a 0.5% increase in the recovery of nickel, copper, and PGMs into bulk concentrate at Talnakh Concentrator.
A smart assistant for flotation machine operators went on stream at Norilsk Concentrator’s copper circuit. The system uses modelling algorithms leveraging intelligent analysis methods and makes recommendations based on statistics and the expertise of flotation machine operators, leaving specialists on the ground to make the final decision. The system’s deployment was launched in 2020. Experts from Norilsk Concentrator and developers of the system worked through all possible scenarios to rule out almost all errors in the assistant’s operation. After pilot tests, the system is expected to work fully automatically. The Company is considering adding a video analytics module to the solution going forward.
In 2023, the Company launched a charge blending optimisation project to stabilise concentrator processes. Tests have shown that predictions based on actual feedstock data, the current process status, and the concentrator’s performance with different types of ore reduce productivity and recovery losses. A preliminary predictive model has been developed so far, with a comprehensive diagnostic of the concentration stage and development of a full‑scale predictive model slated for the first half of 2024 to support pilot tests in a live environment.
Additive manufacturing
The Company is making great strides in developing 3D‑based additive solutions.
In 2023, Nornickel used 3D printing to create and install a large, wear‑resistant cast iron spiral chamber on a pump at Nadezhda Metallurgical Plant. This part is a critical device for lifting concentrate from the ore‑settling tank. Typically, replacing this chamber would take around a year, including the time it takes to create its detailed drawings. However, additive technologies have eliminated this first step through scanning the part and creating its 3D model.
Additive manufacturing reduces the lead times to manufacture and deliver equipment and components by 50%. Additionally, it enables quick changes and the creation of objects of any shape. Three‑dimensional printing can also prevent unscheduled downtime in production and facilitate partial import substitution.
Turbidity monitoring system
Nornickel has introduced a new proprietary technology at Copper Plant – a video analytics system to monitor turbidity of water after ore processing.
The ore mixed with water into slurry is sent from the concentrator to the smelter’s drying shop, where water is separated from the copper concentrate in thickeners. The water discharged from the thickeners must be clear, with no traces of concentrate. The turbidity monitoring system helps to control this.
The process is monitored by video cameras. The data from the cameras are processed by AI‑enabled video analytics software. If the drains are too turbid, the system notifies the operator and records the violation. This reduces the loss of copper concentrate.
Powder metallurgy
Powder metallurgy is an economically beneficial alternative to mechanical processing of various metal parts. It allows for the creation of items with unique properties, significantly increasing metal use efficiency and enhancing the competitiveness of end products.
Demand for powder materials is growing on the back of rapid advances in 3D printing, die casting, hot isostatic pressing, and coating application. Powders can also be used in other innovative developments, from new nickel‑ and cobalt‑based heat‑resistant alloys to catalytic materials.
The first prototypes of powders from nickel alloys for use in 3D printing and hot pressing were obtained by Nornickel back in 2022. In 2023, the Company conducted benchmarking studies and is currently piloting their commercial operation using a 3D printer.
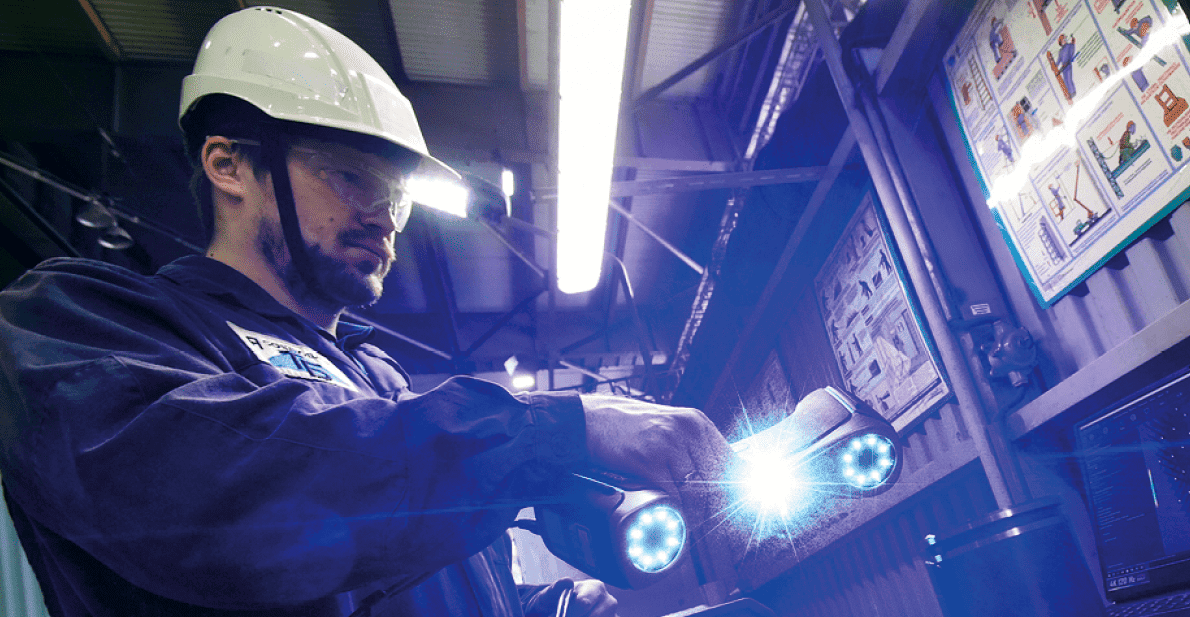
Digital projects
Deployment of innovative tools is a critical lever to improve Nornickel’s business processes and workplace safety. Nornickel has been continuously working towards securing technological sovereignty and developing IT initiatives to support its key business segments.
In 2023, the Company updated its IT strategy. Its key strategic ambitions include reliability and availability, agility and technological sovereignty, while the strategic objectives encompass driving faster decision making, building the necessary capabilities, and ensuring the smooth operation of the Company’s IT landscape during the transformation.
Spending on digital projects totalled RUB 7.6 billion in 2023.
IT infrastructure monitoring
By continuously monitoring key performance metrics, help desks can timely locate issues, prevent information system downtime, and identify opportunities to boost IT landscape performance.
In 2023, the Company continued to develop its corporate IT monitoring function. Over the last year, the number of monitored IT facilities increased by 20% to more than 20 thousand. Today, over 3 million behavioural metrics are collected and analysed on a 24/7 basis, enabling the Company to be more proactive and promptly make informed decisions on IT service management.
Data Lake ecosystem
One of the core elements in the corporate digital landscape is the Data Lake, a scalable platform to digitise operating and business processes, which, in the longer run, will enable storing and analysing data for the entire Group while driving synergies by enriching data in external systems with new data. Integration data flows from Nornickel’s core production sites have already been incorporated into the ecosystem.
A proprietary framework has been developed for the ecosystem for smoother connection and processing of data from equipment sensors based on advanced open source solutions. Existing solutions allow integrating machine‑learning models, generating analytical reports, customising calculations, and running basic quality checks of metrics without developing additional standalone components.
In 2023, Nornickel successfully rolled out the Data Platform PROD landscape based on Russian Arenadata software, which supports a multi‑landscape ecosystem. A geo‑distributed Data Lake infrastructure is slated to be rolled out across production sites in 2024.
Enhancing corporate business processes
A total 38 Group enterprises have adopted electronic document management. Introduction of algorithms and robotic process automation of accounting function tasks have boosted the effectiveness of certain processes by as much as 13 times. As part of implementing electronic document management for the HR function, the system was redesigned to be hosted on the domestic Directum RX platform.
A pilot project to digitise contracts has reduced document signing times, with a record turnaround of just 30 minutes achieved in one of the tests.
Further development of digital treasury Dynamic discounting tools launched in 2023 were used to run 14 tenders for a total of over RUB 300 million during the year. Nornickel has been actively developing its monitoring and analytics landscape to increase process maturity. The necessary enablers have been put in place for the deployment and rollout of a full‑cycle management digital platform, including monitoring and forecasting tools.
Towards the end of 2023, as part of expanding the functionality offered by the supplier online account, the Company introduced dynamic discounting feature to support contract negotiation and execution processes, with the coverage of key suppliers expanded by more than 1 thousand companies operating across the country, or over 30% of the total number of Nornickel suppliers.
In 2023, the Company migrated to a systematic tax monitoring platform to facilitate dispute resolution between the Company and tax authorities. At the time of writing this Report, over 97% of the Group’s sales were monitored by tax authorities in real time. The Company is further increasing the platform’s coverage of Group enterprises, improving its interface, enhancing data quality, and accelerating data sharing while driving integration with information systems of various government authorities.
Nornickel is a top innovation‑driven counterparty demonstrating the maximum level of disclosure and cooperation with the Federal Tax Service of Russia, which already results in preferences granted to it by regulatory authorities.
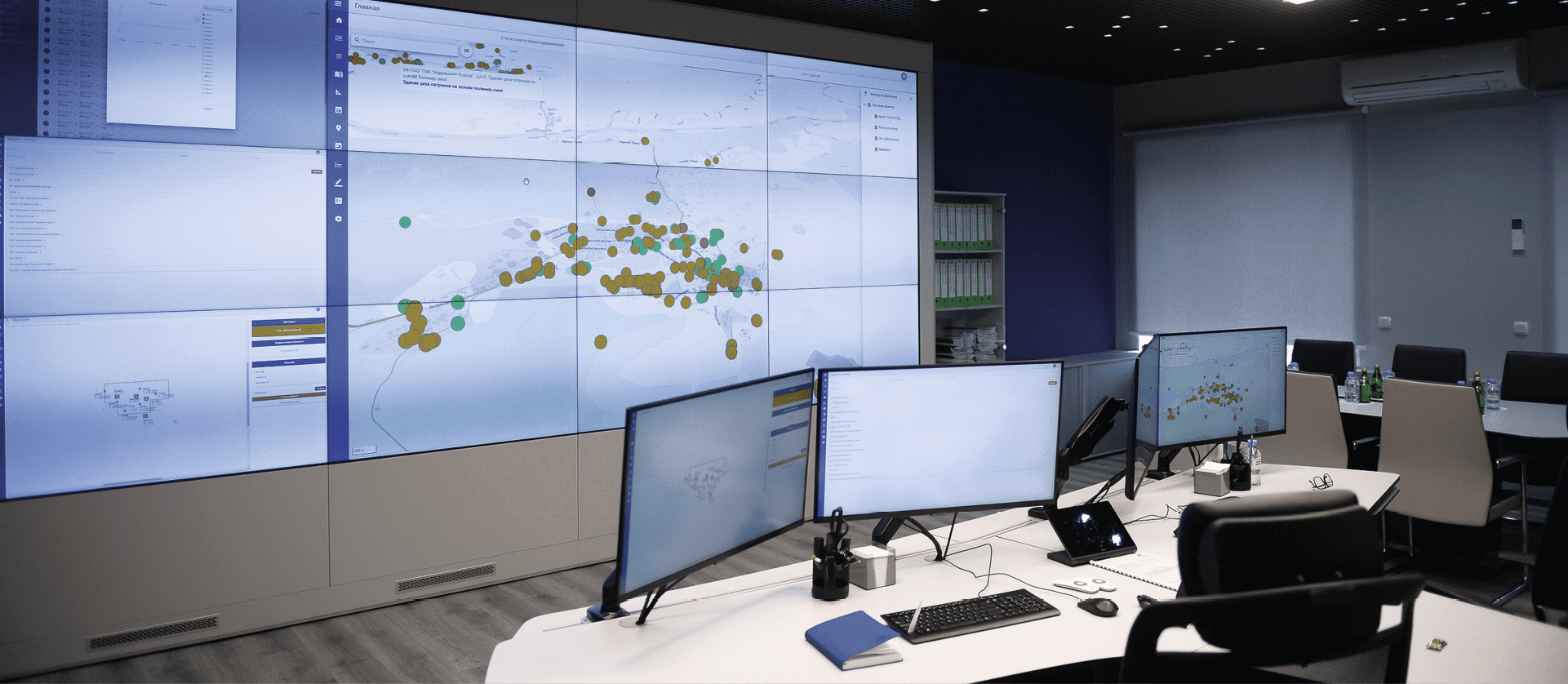