Environmental strategy
In 2020, Nornickel developed its Holistic Environmental Strategy which sets clear goals across key focus areas: climate change, air, water, soil, waste, and biodiversity. The Strategy was further detailed and approved by the Board of Directors in 2021 and updated in the first quarter of 2024.
For more details on the Environmental Strategy, see the Company website.
The updated Strategy is divided into mandatory and voluntary sections. The mandatory part focuses on legal compliance and includes targets across seven key pillars: number of emergencies, air, water, tailings and waste, soil, biodiversity, and stock exchange requirements.
To meet the set targets, the Company developed programmes containing more than 150 specific initiatives.
Key measures include reduction of sulphur dioxide emissions in Norilsk and Monchegorsk; water recycling and reuse; commissioning and retrofit of wastewater treatment at discharge sites; land remediation, clean‑up, and reforestation; monitoring of environmental media and the deployment of an automated pollutant emission control system; and biodiversity impact assessment in all areas affected by the Company’s operations.
The voluntary section of the Strategy includes optional pillars, such as waste (increasing recycling rates), soil, some international initiatives and standards, and climate change – a total of 187 initiatives.
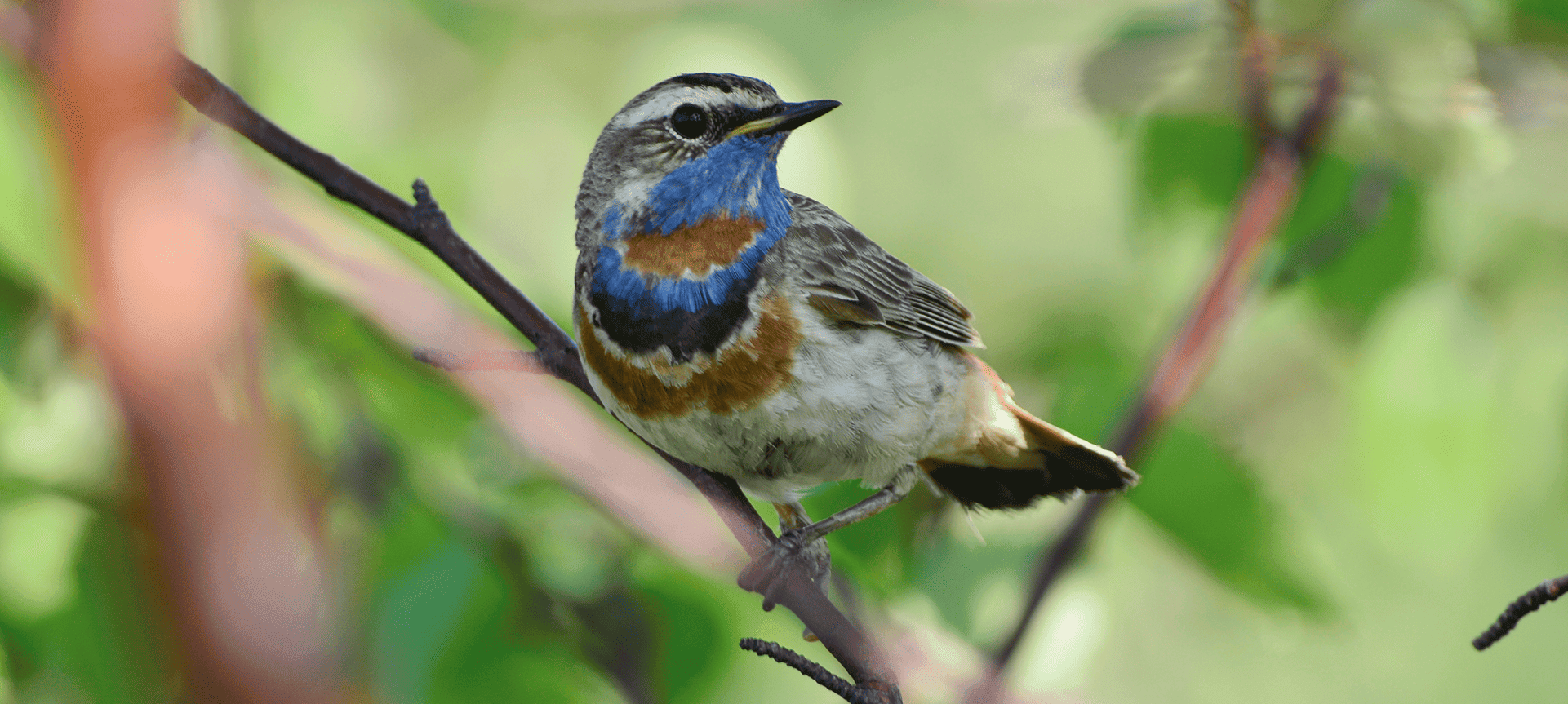
Environmental management
In place since 2005, Nornickel’s Environmental Management System (EMS) is part of the Corporate Integrated Quality and Environmental Management System. This ensures coordination between all environmental matters and other areas, enhancing the Company’s overall performance on environmental safety.
System audit
The Company confirms the EMS compliance with ISO 14001:2015 by engaging Bureau Veritas Certification Rus (BVC), a leading international certification body, to conduct surveillance audits once a year and recertification audits every three years.
Bureau Veritas Certification Rus operates in Russia under the accreditation of the Egyptian EGAC, which is a full signatory and participant of the IAF MLA (the Multilateral Recognition Arrangement of the International Accreditation Forum).
In 2023, the seventh recertification audit of the system confirmed the Company’s compliance with the standard and extended the certification until 12 January 2027.
At the end of 2023, 53% of Group companiesBy average headcount. were certified to this international environmental standard ISO 14001:2015
Climate
Our approach
The Company continues integrating its climate risk and risk factor management system into its business processes in accordance with TCFD and COSO recommendations.
To assess risks and opportunities arising from the global energy transition, Nornickel has developed three own scenarios for global economy and climate change until 2050.
The Company has chosen the Sustainable Palladium as its baseline scenario, according to which traditional industries are expected to remain centre stage along with the growing green economy. In particular, internal combustion engine vehicles are expected to retain a large market share, resulting in a steady long‑term demand for palladium. The other two scenarios are used by the Company to stress‑test climate‑related risks.
Permafrost monitoring
The system developed by Nornickel to monitor permafrost and the facilities built on it enables assessments of the impact permafrost degradation on the Taimyr Peninsula has on the stability of engineering structures while managing related risks.
Climate change in the Arctic drives global‑scale challenges and poses a significant threat to the security of polar infrastructure.
In 2022, Nornickel focused on building a science‑based, practical framework for asset operation management. Deep monitoring wells were drilled in populated areas of the Norilsk Industrial District to study the permafrost soil temperature range and assess the impact of global climate change. A well in the centre of Norilsk, where temperature measurements have been taken since as early as 1958, was restored and fitted with a thermistor string. Data from the well are sent twice a day to the Company’s Facilities Monitoring Centre. Observations showed that in 1958 the base of permafrost was at a 150 m depth, while now it is at 147.7 m. The pace of permafrost thawing at the depth of 10 m was also established: the temperature there has increased by 4.2 °С since record keeping began, which confirms the steady trend of global warming.
In 2023, the Company started to develop a scientific approach to monitoring permafrost and using these data to build mathematical models to assess the impact of natural and anthropogenic factors on permafrost. Cooperation was established with the Research Centre for Construction Technologies and Monitoring of Buildings and Structures in the Northern Arctic of the Fedorovsky Polar State University.
The technical condition of facilities built on permafrost in the Norilsk Industrial District is monitored to reduce the risk of emergencies. To date, more than 1.8 thousand automated sensors have been installed across 218 facilities to gauge soil temperature and displacement of individual elements, carry out an ongoing control of temperature and humidity in crawl spaces, respond to possible failures of heat and water supply systems, monitor for relative deformation of structures, etc.
Sensor readings are sent to the control unit in real time. Along with analysing automated monitoring data, the Centre’s experts run a range of geotechnical surveys, including visual inspections, geodetic monitoring, and measurement of groundwater level and foundation soil temperature.
A new approach based on the methods of mathematical modelling of thermal and mechanical interaction was developed to assess the impact of climate change on the stability of facilities in the Norilsk Industrial District. It relies on the climate change forecast across the Company’s footprint, prepared by leading research institutions. Buildings with foundation on soils that remained frozen throughout construction and operation will be most affected by climate change. That said, one of the key challenges is the lack of information about the properties of soils, which have changed significantly during the operation of structures. To address this issue, geotechnical surveys and laboratory studies of frozen soils have been carried out to collect the necessary data.
Background monitoring
Nornickel was the first Russian organisation to set up its own regional system of background permafrost monitoring. The data obtained can be used to supplement the database on the condition and changes of permafrost in the natural environment, quantitatively predict changes in permafrost conditions, and assess natural and anthropogenic impacts on the soil temperature.
To date, studies have covered an area stretching about 147 km from the Norilsk Industrial District to Dudinka and measuring about 8 thousand sq km, and identified 11 testing grounds that best reflect the diversity of landscape and geocryological conditions. In 2023, the Company awarded contracts to drill 24 wells with a depth of 10 to 20 m and two wells with a depth of 200 m on the allocated testing grounds to assess permafrost characteristics and determine the parameters of terrestrial heat flow. The project was awarded the National Environmental Prize named after V.I. Vernadsky.
Thus, the Company now has geotechnical and background monitoring data that support informed and economically sound decisions regarding further operation of assets.
Greenhouse gases
In 2023, direct and energy indirect GHG emissions from operations (Scope 1 + 2) that could not be potentially removed by the Company amounted to 8.6 mln t, without the possibility of the process of absorbing greenhouse gas emissions in the Company.The emissions were calculated using the location-based method, including the emissions allowance for the Sulphur Project and excluding emissions from heat and electricity supplies to household consumers.
The year‑on‑year decrease in GHG emissions (Scope 1 + 2) was due to:
- lower per unit fuel consumption for electricity generation as a result of optimising equipment operation modes at combined heat and power (CHP) plants
- higher share of HPPs in the power generation mix due to the overall optimisation of the energy system’s operation
- less diesel fuel burnt at CHP plants in 2023 year‑on‑year.
Energy indirect GHG emissions (Scope 2) were calculated using the location‑based method, including regional emission factors. Notably, the Trans‑Baikal Division and RusHydro signed a bilateral agreement to purchase 212.1 mln kWh of electricity generated by RusHydro hydropower plants, up 20% y‑o‑y. This reduced Scope 2 GHG emissions by more than 200 kt of CO2 equivalent in 2023.
Nornickel is exploring opportunities for climate projects to reduce the impact of its operations on climate. To this end, the Company signed an agreement with Siberian Federal University to conceptualise approaches to implementing a comprehensive environmental and climate project.
The Company has also developed an innovative solution to utilise waste from its core operations to remove GHG carbon dioxide (CO2). By extracting materials from mines and bringing them to the surface, the Company already creates conditions for mineralisation, which is a natural carbon dioxide absorption process.
Concentrators fine grind ores and separate useful elements from gangue – tailings. The tailings then undergo special treatment and are transported to tailings storage facilities to be distributed over the entire surface, which enables their reaction with atmospheric carbon dioxide. During mineralisation, minerals contained in Nornickel’s ores react with carbon dioxide to form stable secondary carbonates, which remain in the tailings storage facility.
The tailings from ore concentration can chemically capture from 4.5 to 17.9 kg of CO2 per tonne of tailings in the natural environment, depending on the mineral composition of gangue.
Calculations based on natural mineralisation studies conducted in 2022 and 2023 showed that about 300 kt of CO2 per year has been removed. The Company is currently developing a methodology to estimate and account for this absorption capacity of tailings, which, once audited and verified by an external auditor, will be incorporated in the Company’s statements on GHG emissions and removals.
The Company’s further research is focused on developing a technology for accelerated and artificial mineralisation. Such a technology will significantly increase the absorption capacity of tailings as compared to natural mineralisation and, when implemented at all Company sites, reduce the carbon footprint of products in the long term.
In 2023, Nornickel submitted a Report on GHG Emissions to the Russian Ministry of Economic Development to include its data in the GHG emissions registry.According to Federal Law No. FZ-296 On Limiting Greenhouse Gas Emissions, dated 2 July 2021, starting from 2023, emitters generating 150 kt of carbon dioxide per year or more must submit annual reports on their GHG emissions by 1 July of the year following the reporting year. The calculations only include direct GHG emissions and are made as per Order No. 371 On Approval of Methods for Quantitative Determination of Greenhouse Gas Emissions and Greenhouse Gas Removals, dated 27 May 2022.
In addition, the Board of Directors approved Nornickel’s Key Focus Areas of Carbon Neutrality, outlining key steps to reduce gross GHG emissions and carbon footprint of products over short‑, medium‑, and long‑term horizons. The document emphasises development of low‑carbon energy sources and climate projects, the use of energy‑efficient technologies and equipment, artificial intelligence, and conversion of vehicles to alternative fuels. The Company also continues looking into opportunities for CO2 capture and utilisation projects and unregulated bilateral power purchase agreements.
Nornickel’s key production facilities are located in the Norilsk Industrial District, in the Arctic Circle, and operate in sub‑zero temperatures for about eight months of the year. The district is isolated from the federal energy infrastructure, so Nornickel generates electricity and heat locally at its own generating facilities (100% owned by the Group). As a result, the bulk of GHG emissions comes from the Company’s energy assets. As Nornickel is the only producer of electricity and heat in the Norilsk Industrial District, the Company also fully meets the demand for energy and heat from social infrastructure facilities and the local population. The share of GHG emissions generated by infrastructure facilities and households in Nornickel’s regions of operation is on average 12% of total Scope 1 + 2 GHG emissions.
Scope 3
The Company annually quantifies its other indirect (Scope 3) GHG emissions, which originate outside the Group and are beyond the Group’s control or influence. The Company distinguishes between upstream and downstream Scope 3 emissions.
The bulk of upstream Scope 3 emissions is related to the purchase of raw materials and equipment from suppliers as well as energy and fuel consumption (to the extent not included in Scope 1 + 2). Upstream Scope 3 emissions have been primarily impacted by lower diesel fuel consumption for power generation in the Norilsk Industrial District and by the sale of NordStar Airlines in 2022.
Downstream Scope 3 emissions come mostly from transportation and processing of intermediates sold outside the Group – iron ore and copper concentrates produced by the Trans‑Baikal Division and nickel intermediate products. Downstream Scope 3 emissions are influenced by changes in sales volumes, the Group’s product and customer portfolio, and the geographic mix of product sales. In 2023, these emissions increased year‑on‑year mostly due to higher sales of intermediates.
Scope 3 emissions are quantified in line with the GHG Protocol guidance for all categories relevant to the Group and the IPCC Guidelines for National Greenhouse Gas Inventories.
Energy sources and energy efficiency
The Company’s key renewable energy source is hydropower generated by the Group’s Ust‑Khantayskaya and Kureyskaya HPPs. In 2023, the share of renewables in total electricity generation stood at 55% for the Group and 58% for the Norilsk Industrial District. The share of renewables in the Group’s total electricity and fuel mix was 12%.
Nornickel has its own energy assets located in the Norilsk Industrial District. Natural gas and renewables (hydropower) are the core low‑carbon sources for energy generation. Diesel fuel, fuel oil, petrol, and jet fuel are used by Nornickel’s transport assets. Use of coal by energy assets is minimised to only small amounts in certain production processes.
The use of other renewables, such as solar and geothermal energy, is impracticable as Nornickel’s core operating assets are located in a region with harsh climatic conditions.
Due to harsh climates, not all renewables are available in the Arctic Circle
The Group’s own energy assets produce about 54% of total energy and 90% of electricity consumed by the Group. The Company also supplies electricity and heat to external consumers, primarily local social infrastructure and local communities in the Norilsk Industrial District.
The Group attaches great importance to improving the energy efficiency of its existing and future production sites, focusing on keeping GHG emissions within the targets announced in its comprehensive environmental programme. In 2023, the Company invested more than USD 400 million in upgrading its energy infrastructure. The investments cover multiple projects related to equipment replacement at thermal and hydropower plants and upgrades to fuel tank storage facilities, power grids, and gas pipelines. In 2023, 45 energy‑saving initiatives were implemented.
Air
High sulphur dioxide emissions from the smelting of sulphide concentrates with high sulphur content are a key environmental issue for the Company.
Our targets
Nornickel’s strategic plan is to transform the Company into an environmentally clean and safe business by implementing Sulphur Project 2.0 across the Norilsk and Kola Divisions and thus cutting its sulphur dioxide emissions.
In 2023, the Group’s pollutant emissions totalled 1.7 mln t, down 6.1% y‑o‑y. The decline was due to lower sulphur content in metal‑bearing feed.
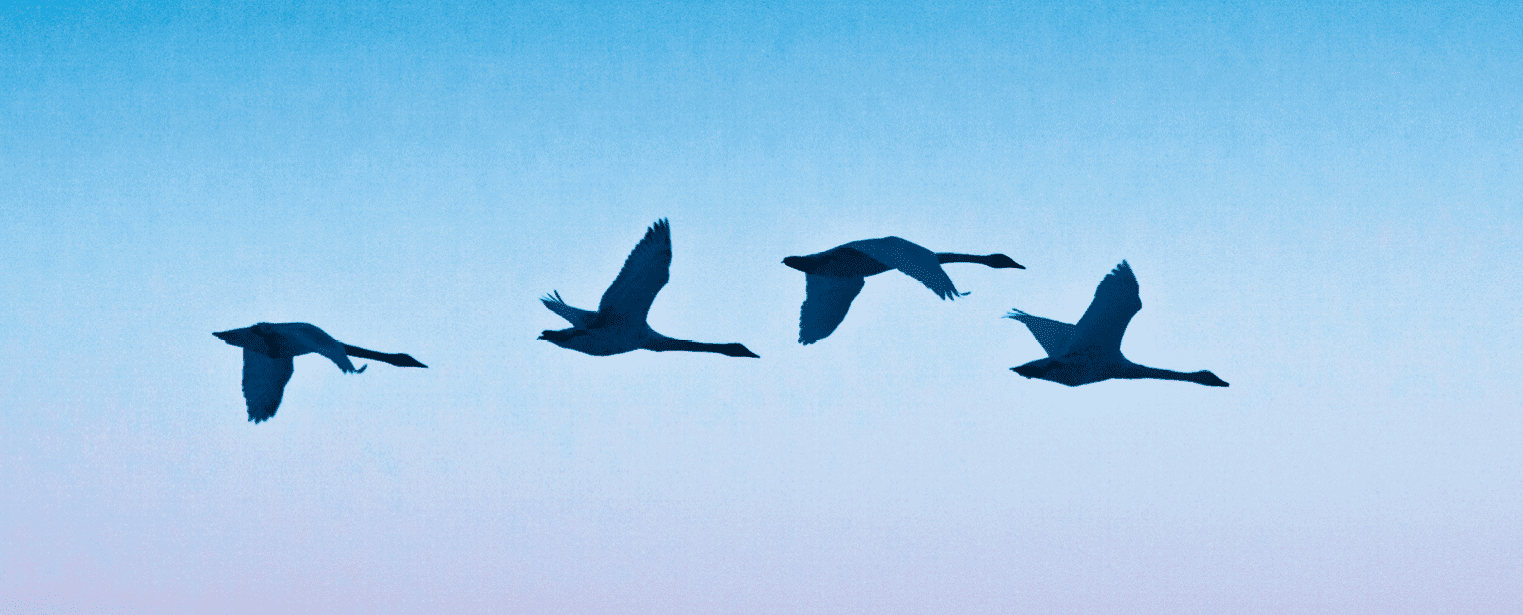
Water
The Company’s assets are located in regions with sufficient water resources. In 2023, as in previous years, no shortage of water was reported as enterprises and households were supplied with sufficient amounts of water.
Nornickel is committed to responsible and sustainable use of water resources and prevention of water body pollution. To this end, the Company regularly monitors groundwater at production facilities and designs water collection and treatment systems.
The Company is extremely careful about its use of fresh water and strictly complies with restrictions applicable to industrial water withdrawal.
Nornickel’s key production facilities use closed water circuits to keep clean water withdrawal on a relatively low level. Furthermore, the Company never withdraws water from protected natural areas. The water we use is mostly withdrawn from surface and underground water bodies, in addition to third‑party wastewater and natural water inflow. Water withdrawal in 2023 decreased by 38 Mcm y‑o‑y, including a 17 Mcm decrease in fresh water. This was due to the launch of automated systems for energy metering, savings in water consumption, and variable water withdrawal for cooling CHPP equipment. Natural water inflow accounted for 16.3% of total water withdrawal in 2023. All facilities using water have programmes in place to monitor water bodies and water protection areas.
In 2023, 83% of all water used was recycled or reused, in line with the Company’s strategic goals.
Wastewater discharge into water bodies primarily stays within the approved limits and has no material impact on biodiversity of water bodies and related habitats. In 2023, the Company decreased its total wastewater discharge by 12.5% y‑o‑y, with untreated wastewater discharge unchanged year‑on‑year. In 2023, the mass of pollutant discharges decreased by 25% y‑o‑y to 157 kt.
The Company routinely partially reuses its produced and mine waters in production, particularly at concentrators, and in sulphuric acid neutralisation under the Sulphur Project.
Nornickel strives to comply with legal requirements for pollutant concentrations in wastewater. All domestic sewage discharges are treated at biological or mechanical and chemical treatment facilities to ensure that water quality meets accepted standards. All programmes at the Company contain measures to this end.
The Company’s regular measures to assess its impact on water resources include:
- wastewater inventory
- assessment of wastewater quality at accredited laboratories as often as required by laws
- monitoring of wastewater discharge volume and quality at discharge sites
- observation of surface water bodies at control points upstream and downstream of discharge sites
- investments in improving the performance of water treatment systems and building new systems
- monitoring of wastewater treatment processes at treatment facilities and implementation of organisational and technical measures to improve treatment effectiveness.
Waste
Over 99% of the Company’s generated waste is mineral and non‑hazardous. Such waste includes rock and overburden, tailings, metallurgical slags, and ferrous cake.
Ore extraction waste is placed in tailings and used as backfill for underground workings and open pits, road fill, or for tailings dam reinforcement. In total waste generated, gangue accounts for 80%, tailings 17%, and recycled/reused waste 19%.
Total waste generation increased in 2023 due to the development of the Mokulayevskoye limestone deposit.
Tailings
Today, Nornickel operates six tailings storage facilities: four in the Norilsk Division, one in the Kola Division, and one in the Trans‑Baikal Division.
While all tailings storage facilities operated by the Company are located at a significant distance from production facilities and local communities, Nornickel recognises these facilities as higher‑risk assets with significant potential environmental and social impacts. This is why the Company has in place the Tailings Management Policy, regularly monitors the condition of hydraulic structures, and inspects discharge sites as well as adjacent areas.
Biodiversity
Although Nornickel has been focused on supporting protected areas in its regions of operation for years, it was not until 2022 that the Company decided to establish a dedicated biodiversity impact management system. This led to first baseline surveys, which became another milestone in Nornickel’s history of partnering with research institutions for biodiversity conservation.
and the Biodiversity section on the Company website.The baseline survey project, known as the Big Scientific Expedition, is a comprehensive study of the ecosystems near the Company’s mining, production, and energy facilities. Phase 2 of the Expedition covered three regions: the Zabaykalsky Territory, the Murmansk Region, and the Taimyr Peninsula. This biodiversity survey became the most extensive ecosystem study since the Soviet era.
Nornickel created the life.nornickel.com website to tell about its biodiversity conservation projects and individual measures taken in clear and simple language.
Phase 2 of the Big Scientific Expedition brought more detailed delineation of the areas where ecosystem biodiversity is exposed to impact from our operations. New data were also used to update the methodology for calculating the integrated ecosystem health indicator(IEHI), which will be used in assessing progress towards the goal of net‑zero biodiversity loss. Changes in the IEHI can also confirm biodiversity net gain where it is achieved. In addition to refining the boundaries and methodology for calculating the IEHI, the 2023 surveys established which negative impacts from operations affect the surrounding ecosystems.
The scientists used the latest research methods, molecular genetic and phytochemical, and seamlessly integrated the results into the existing methodology for calculating the IEHI. The molecular genetic studies also discovered a new weevil species near Norilsk, which Norilsk residents called “putoranchik” after the Putorana Plateau, and a lot of new Myxogastria species in the Zabaykalsky Territory.
The team also studied how heavy metals migrate from rock dumps and proved that such migration does not affect plant diversity: the dumps were initially set up in areas with increased natural content of heavy metals in soils, so their leaching does not have a negative impact on plant and soil ecosystems as they are adapted to increased heavy metal concentrations in soils. Such adaptability is characteristic of places where ore bodies lie very close to fertile soil layers.
The next step in developing a biodiversity impact management system is to use the baseline study results to finalise the draft corporate Standard for Ecosystem Biodiversity Conservation and Monitoring and divisional biodiversity conservation and monitoring programmes and incorporate them into short‑term biodiversity conservation action plans (measures). The draft standard describes how impacts on biodiversity are managed, while conservation and monitoring programmes contain information on division‑specific biodiversity aspects. All this information feeds into action plans (measures) for biodiversity conservation. The documents are expected to be finalised and approved within a year of the end of the last, third, phase of the Big Scientific Expedition.
Studies to improve the productivity of Lake Pyasino through guanotrophication were another separate project, now in its second year.
Nornickel also signed an agreement with the Russian Ministry of Natural Resources and Environment to preserve the gyrfalcon population in Russia, starting this effort in 2023.
Cooperation with nature reserves
There are no nature reserves in the proximity of Nornickel’s operations. In the Murmansk Region, the Pasvik and the Lapland Nature Reserves are 10 to 15 km away from the Kola Division production facilities. In the Krasnoyarsk Territory, the boundaries of the Putoransky Nature Reserve buffer zone are at a distance of 80 to 100 km from the Norilsk Division production sites.
In 2023, Nornickel environmentalists, expedition participants from the Siberian Branch of the Russian Academy of Sciences, and representatives of the nature reserves wrapped up the second year of the Big Scientific Expedition. The expedition covered the areas around Nornickel’s mining and processing operations. Its key feature was collaboration between researchers and scientists from the nature reserves who have the most complete statistical data on biodiversity within their respective areas over the past decades.
In line with its long‑term strategy to maintain biodiversity in its regions of operation and preserve the unique Arctic nature, the Company also organises regular volunteer campaigns, supports nature reserves, and finances studies on Red Data Book animals.
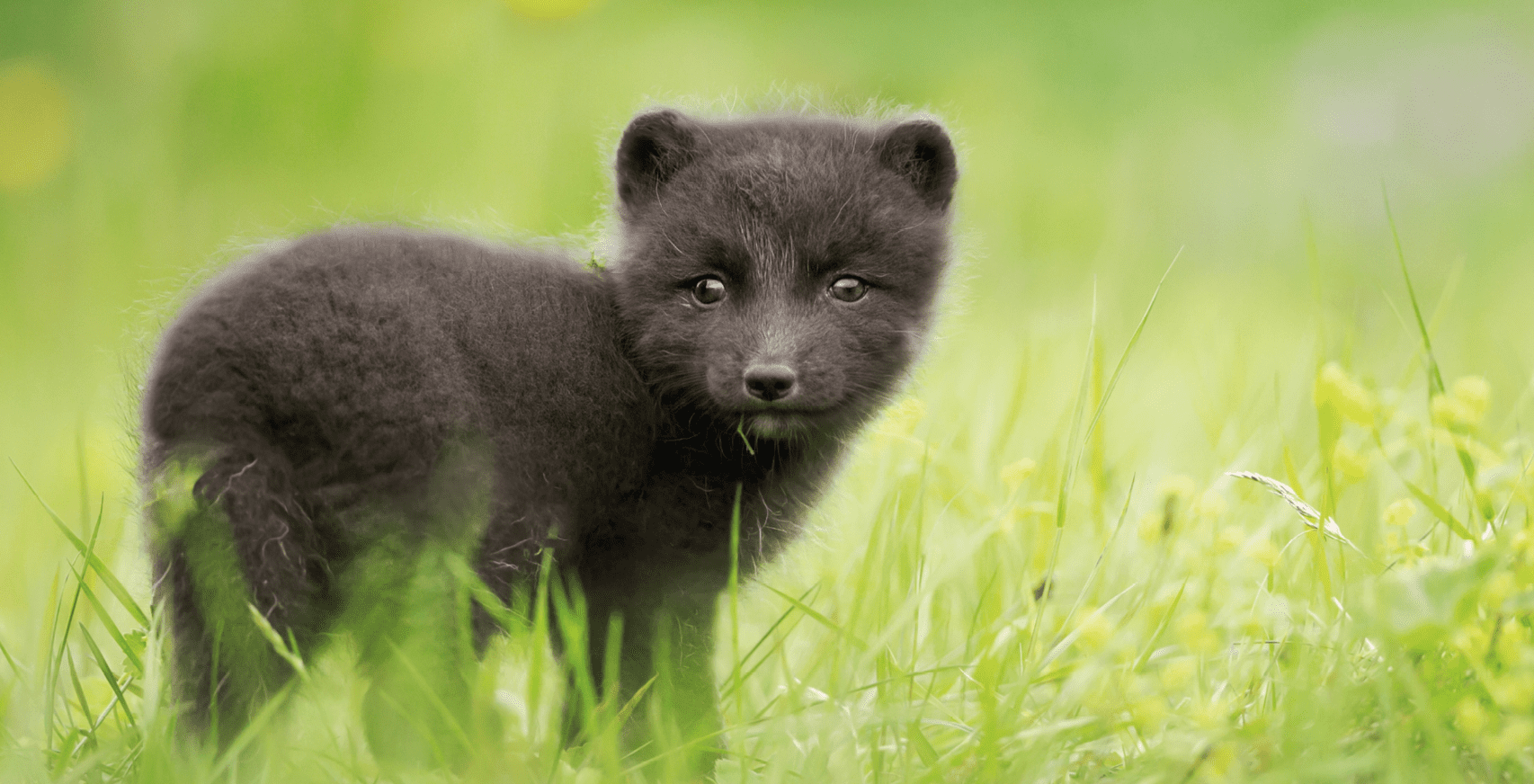